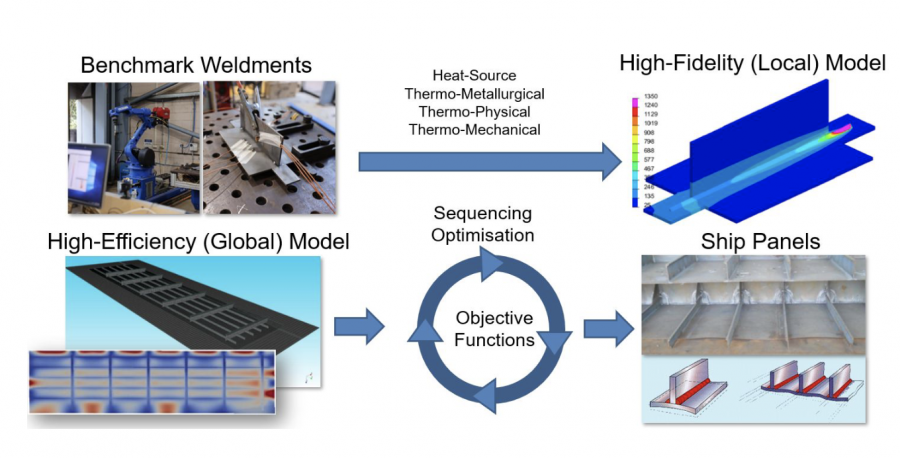
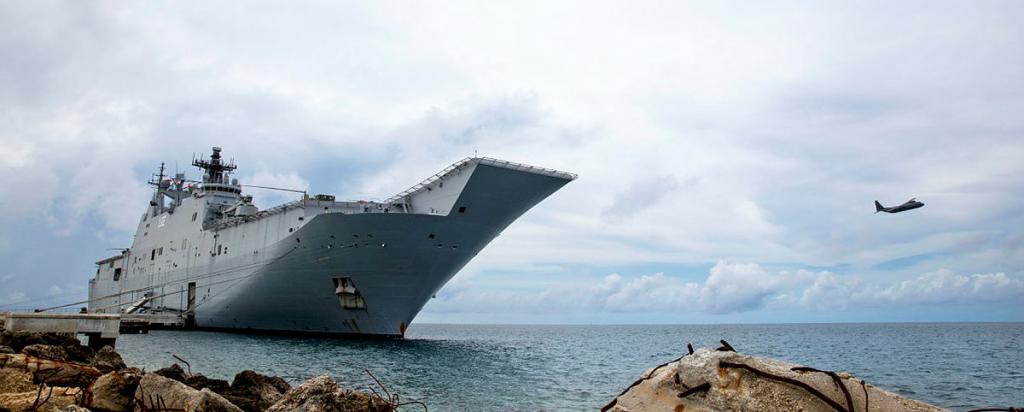
Multiphysics simulations for advancing Australia’s shipbuilding technology
ANSTO is working with BAE Systems Maritime Australia, and the University of Wollongong under the auspices of the DMTC Ltd. on the development of multiphysics numerical simulations capable of capturing thermo-physical, thermo-metallurgical and thermo-mechanical processes taking place during welding.
Welding leads to localised heating, which then brings about an uneven expansion and contraction of heated material that ultimately results in non-uniform residual stresses and distortion of the welded components, such as large ship panels.
Furthermore, in the case of low-alloyed steel, which is extensively used for shipbuilding, the welding processes also significantly alter the microstructure of the material— affecting its mechanical properties.
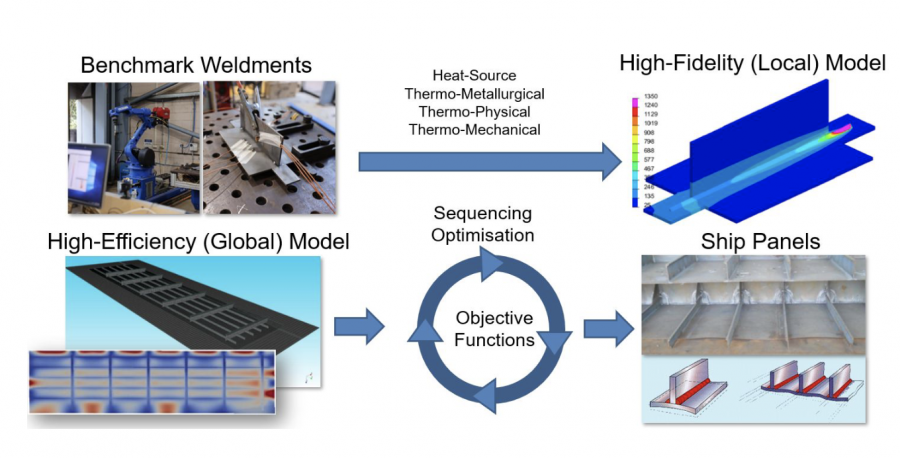
ANSTO has developed high-fidelity numerical simulations capable of accurately predicting welding-induced constituent phases, residual stresses, and distortion, which affect the performance of welded components during their service life.
Material scientists at ANSTO are also developing high-efficiency numerical simulations, which could significantly speed up the optimisation of the weld sequencing and thereby improve process quality and efficiency through advanced automation.
The weld sequencing optimisation will take advantage of novel optimisation algorithms and machine learning techniques to identify the welding sequencing leading to the desired weld properties, while minimising the post-weld residual stresses and distortion.
ANSTO together with its industrial and academic partners aims to improve manufacturing practices in shipyards via advanced numerical simulations, which are key in enhancing robotic welding capabilities and manufacturing processes in shipbuilding.