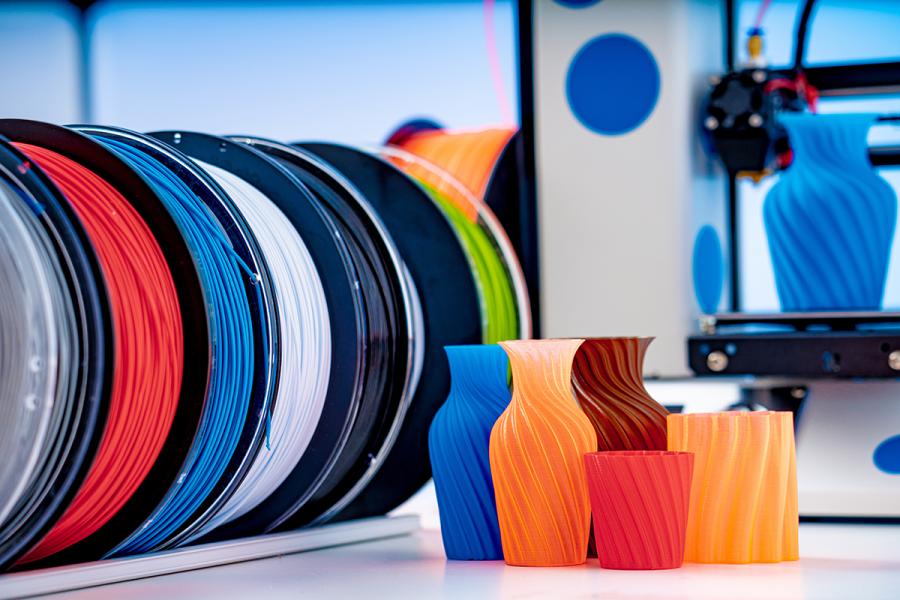
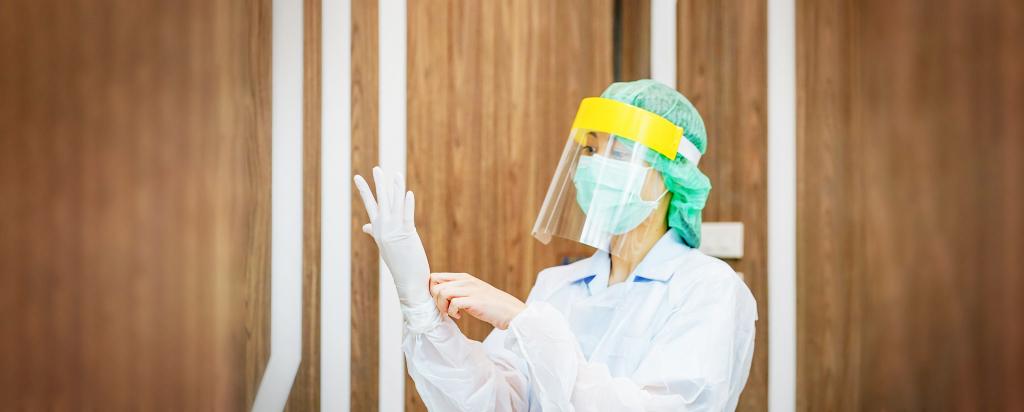
Published on the 27th October 2022 by ANSTO Staff
ANSTO is collaborating with additive manufacturing company 3RD Axis on the design, materials and process development of a key ceramic component for an innovative process to convert plastic waste from personal protective equipment (PPE), such as face masks and gowns, into feedstock for 3D printing.
The goal of the project is to use raw materials in discarded or out-of-date PPE, such as masks and sterile wraps, as feedstock to produce polymer filament for digital 3D printers.
“It is normal now for all of us to wear PPE in our everyday lives, which provides protection from airborne contaminants, but it also creates the problem of increased waste and landfill,” said 3RD Axis Director Ashish Jain.
“We are excited to be sharing ANSTO expertise and capabilities in materials development and characterisation to support this promising solution to recycle waste and produce a consumable product in great demand in additive manufacturing,” said Dr Robert Acres, Commercial Technical Consultant, ANSTO.
3rd Axis, a member of ANSTO’s innovation centre, nandin, was awarded two NSW grants to progress the technology. An initial grant was awarded from the NSW Small Business Innovation and Research (SBIR) program in late 2021 to complete the phase 1 feasibility study that was submitted for assessment by the Office of the Chief Scientist and NSW HealthShare SBIR team in April.
Phase 2 of the program is the proof-of-concept stage, which was approved for progression based on the quality of the feasibility study, and a subsequent SBIR grant was awarded this month.
ANSTO worked on the feasibility stage of the project following the awarding of the first grant and completed initial material characterisation to validate the waste separation process, which will provide the raw material the extruder will use to make filaments.
The technology had to provide clean, separate core element materials from the PPE feedstock.
This ceramic screw plastic extrusion machine has been provisionally patented by 3rd Axis.
The unique design of the ceramic extruder makes it different to existing steel extruders that require high-wattage heating elements.
“What we are seeking to do is to take these materials out of the single-use economy and transform them into a durable manufactured article that has a longer life cycle as the next product,” said 3RD Axis Chief Executive Officer Andrew Cooper.
“We are using a triple helix approach to research, development and commercialisation of our products, and the SBIR is a great example of Government, Industry and researchers collaborating to reach a common goal that will provide jobs and opportunity to address a very serious challenge in waste management for the healthcare sector globally,” he added.
3RD Axis is collaborating with medical waste industry partners to streamline collection and separation processes that can be used in hospitals, medical centres, hotels and emergency services vehicles.
It is estimated that 1.6 million tonnes of plastic waste a day has been generated globally since the start of the pandemic outbreak, and 3.4 billion single-use facemasks are discarded daily as a result of COVID-19 safety measures.
In addition to recycling PPE, the technology being developed by 3RD Axis opens the possibility of recycling other plastics and materials.