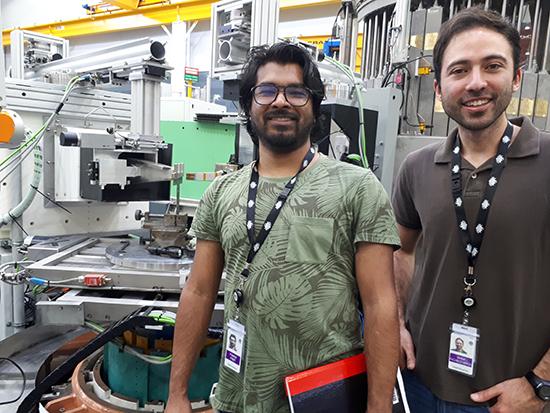
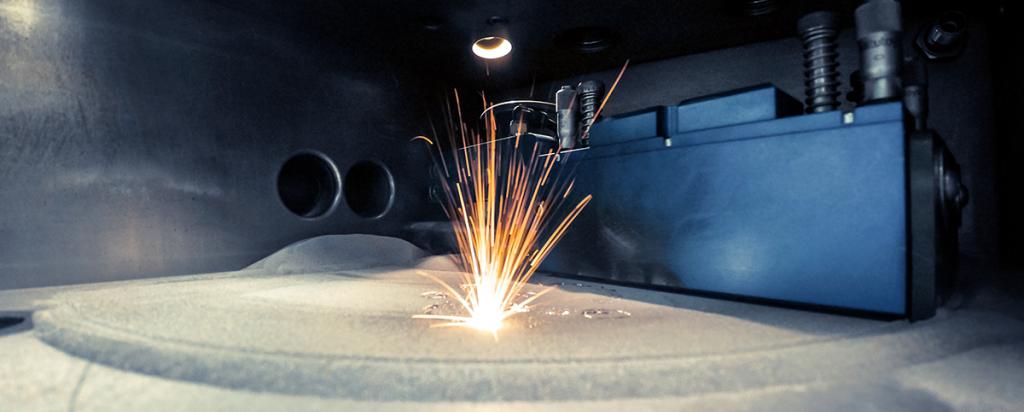
Published on the 7th October 2020 by ANSTO Staff
Key Points
-
The development of an accurate and beneficial tool to assess how complex part geometry influences the development of stresses using the powder bed fusion method will contribute to the use of additive manufacturing for the production of metallic parts in an accurate and predictable manner
-
In manufacturing a simple, L-shaped part, the horizontal orientation showed the least amount of stresses in all three directions
-
Residual stresses in the interior of the parts were measured using the Kowari strain scanner
Studies of the residual stresses that are formed during an additive manufacturing (AM) process have revealed that the build orientation of the part being produced has an impact on the formation of adverse stresses.
The development of an accurate and beneficial tool to assess how complex part geometry influences the development of stresses using the powder bed fusion method published in a study in Additive Manufacturing will contribute to the use of additive manufacturing for the production of metallic parts in an accurate and predictable manner.
As part of an international collaboration led by the Linköping University in Sweden, the investigators, who included Dr Vladimir Luzin at ANSTO, concluded that a careful selection of the printing orientation is important and had a significant impact on the magnitude of residual stresses and, therefore, the potential distortion of the AM part.
In general, a high level of tensile residual stresses can lead to a crack during printing, while at the same time stresses can contribute to deformation in the part.
Both result in the material being scrapped if dimensional tolerance/distortion is compromised or cracking occurs.
However, assuming some optimal conditions for a particular shape, all the effects on unwanted distortions can be eliminated.
Since the variety of shapes is huge, one particular shape, L-shape, was chosen to study the effects of a build-up orientation.
Three experimental approaches were used to characterise the residual stresses in L-shaped parts made of Inconel 781, a material that is important in the energy and aerospace industries, because it has good mechanical properties at high temperature.
X-ray diffraction measurements were used to characterise surface stresses and laser scanning techniques measured overall distortions associated with separating the samples from the base plate.
However, neutron diffraction was necessary to measure residual stress in the interior of the samples due to the high penetration of neutrons.
The Linkoping University team used non-destructive neutron diffraction on the Kowari strain scanner to measure and characterise residual stresses within the bulk of nickel-based superalloy samples to study the effects of sample AM build-up orientation.
The part printed in a horizontal orientation showed the least amounts of stress in all three directions, showing the way for optimisation of the build-up of generic L- shapes.
However, in all orientations, there was a general tendency for compressive stress at the centre of the part.
Tensile residual stress was observed near the surface in all samples, which appears to be potentially problematic and needs to be addressed.
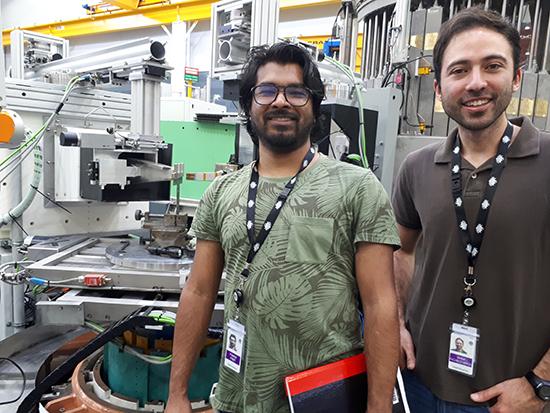
Prabhat Pant and Victor Pacheco Gimon at the Kowari strain scanner for the residual stress measurements
“There is a certain effect of the build-up orientation in the formation of the residual stresses and, therefore, on the performance of the AM parts,” said Prabhat Pant, a PhD student from Linköping University who was supported by the Swedish Foundation for Strategic Research (SSF).
His training mission, supported by the agency, was to carry out research abroad in preparation for the expected start-up of the European Spallation Source, the world most powerful neutron source.
The local supervision at ANSTO was provided by Dr Vladimir Luzin from the Australian Centre for Neutron Scattering.
“Being able to predict critical areas where they will occur, in order to reduce them, is a significant production advantage,” - Prabhat Pant
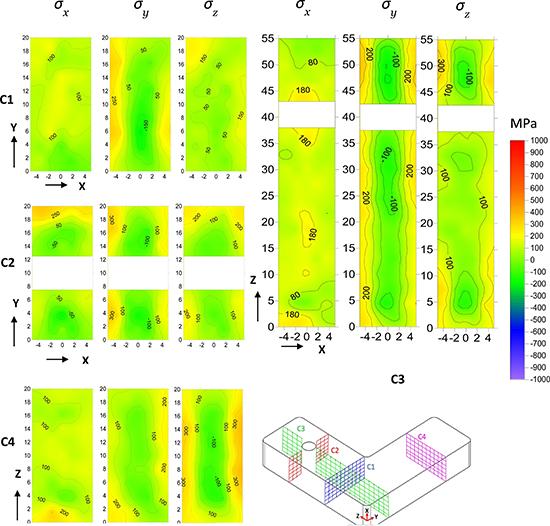
Stress distribution at different cross sections for the horizontally-built sample
“Although these residual stresses can be modified with post processing techniques, the role of residual stress during build up is essential to prevent distortion or cracking at any moment during the manufacturing process.”
The research included the development of a simplified simulation technique using finite element analysis for predicting residual stresses based on part geometry, which, when verified with neutron experimental results, was in a good practical agreement.
However, the investigators noted there was a complex interconnection of the residual stresses in the as-built state for the parts with the orientation of the part, and the geometry of the built-up part.
”We gained a better understanding of how build orientation, the support structure and stress concentration contribute to the development of residual stresses during the laser bed fusion process,” said Pant.
More work is planned to investigate how different scanning strategies and laser power influence the development of residual stresses.