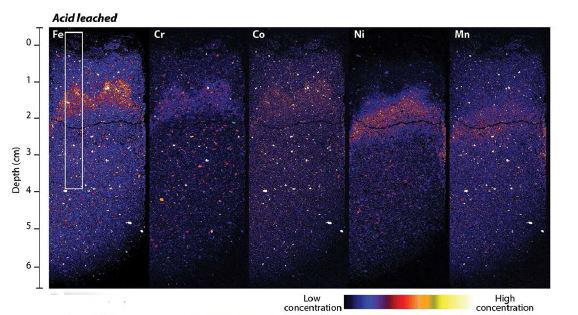
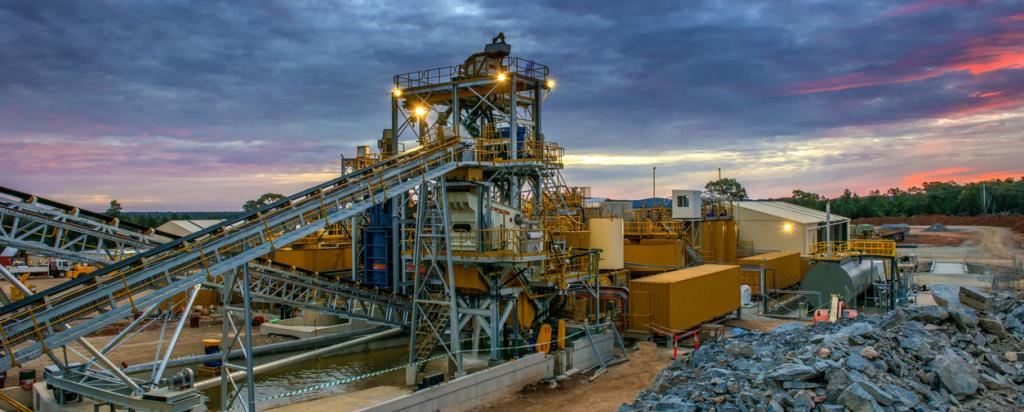
Published on the 11th September 2020 by ANSTO Staff
Key Points
-
Accelerated carbonation of mining waste significantly increases carbon capture for environmental benefit and has the potential to recover valuable minerals, such as nickel and cobalt, for economic benefit
-
Two approaches using existing low cost and low energy technologies to accelerate carbonation demonstrated significant carbon capture over a very short period and the formation of carbonate minerals
-
Images from the X-ray fluorescence beamline at the Australian Synchrotron revealed visual microscopic evidence of the distribution of trace metals and other key changes to the microstructure
Collaborative research that has significant potential benefits for the mining industry and carbon capture was the focus of Dr Jessica Hamilton’s winning presentation in the Australian Falling Walls Lab competition this week.
Their paper published by a large international collaboration led by Monash University in Economic Geology describes laboratory experiments to evaluate two approaches using existing low cost and low energy technologies to reuse stockpiled waste from mining operations and capture carbon dioxide in the form of valuable carbonate minerals.
Although passive carbonation of mine tailings occurs naturally, the equivalent of approximately 30 years of passive carbonation was achieved within four weeks in one of the experiments.
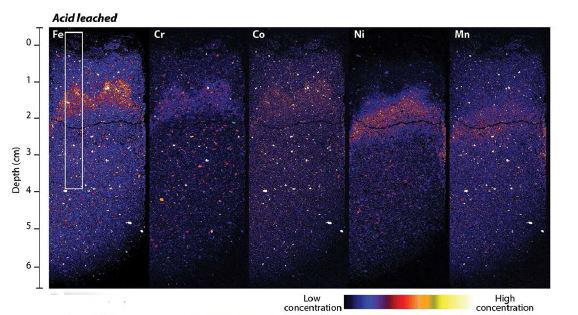
The location and concentration of Immobilised iron, chromium, cobalt, nickel and manganese in treated tailings as shown by coloured areas in XFM images
“If you can integrate carbon capture with recovery of previously inaccessible minerals, say of nickel and cobalt, you could make some lower grade mines more viable,” said Hamilton.
According to a recent report in Science, today some 419 million tonnes of ultramafic and mafic (rich in magnesium and calcium) waste are produced annually with the potential, if fully carbonated,to lock up 175 million tonnes of atmospheric CO2 per year.
In the study, Hamilton and her associates used laboratory experiments to trial two geochemical treatments to accelerate the carbonation of ultramafic mine tailings at ambient temperatures and pressures.
The first experiment involved a direct reaction of partially saturated tailings from a derelict chrysotile (asbestos) mine in NSW with a simulated mining flue gas, containing 10 percent CO2 in dinitrogen.
This accelerated CO2 sequestration occurs by targeting a highly reactive mineral, brucite (Mg(OH)2), in the tailings.
Investigators noted some limitations on carbonisation with brucite that are linked to water content and humidity.
In the second experiment, the investigators simulated a heap leaching treatment using laboratory columns.
“If we irrigate the mineral waste from mines with acid, the minerals dissolve to produce a solution that is rich in magnesium and calcium, which, in turn, react with CO2 and form solid carbonate minerals,” said Hamilton.
The investigation involved X-ray fluorescence microscopy (XFM) at the Australian Synchrotron, undertaken by Hamilton and XFM Principal Scientist Dr David Paterson, which provided visual microscopic evidence of the distribution of trace metals and other key changes to the microstructure following leaching with diluted sulfuric acid.
XFM (see image above) revealed immobilised iron, chromium, cobalt, nickel and manganese at different depths in the column with the greatest concentration in the region where the pH of the acidic leaching solution was neutralised.
“The real power of XFM was that it allowed us to look at the distribution of elements at a really fine scale and look at the coatings on grains, and the localised geochemical environments where metals were precipitating,” said Hamilton.
The heap leaching produced a liquid high in magnesium capable of sequestering an amount of carbon dioxide 200 times greater than the passive carbonation that occurred at the derelict mine.
“The choice of approach depends on the resources available at the mine and the local mineralogy,” said Hamilton.
“If there is waste acid available and you don’t have much active brucite, then heap leaching is a great option. If there is a CO2 source, and you have brucite, then you might go for direct reaction with that gas. But the two can also be used together, for example, heap leaching can be followed by reaction of the magnesium rich fluids with a CO2 source,” said Hamilton.
An added benefit is that for mines or mineral processing that produces acid as a by-product, this acid can be used and neutralised.
The approach is suitable for waste from platinum, chromite, diamond, some nickel, copper, and historical chrysotile mines.
A testing program is now underway to scale up carbon mineralisation technology at diamond mines in Africa and Canada.
Although Hamilton is now working as an instrument scientist at the Australian Synchrotron, she continues to stay actively involved in the research.
Work is ongoing by A/Prof Siobhan ‘Sasha’ Wilson at the University of Alberta, Prof Gordon Southam at the University of Queensland and Prof Gregory Dipple at the University of British Columbia; all are co-authors on the paper.
Their work on using industrial waste to turn carbon dioxide into stone was recently featured in an article,' The Carbon Vault', in Science.
A study exploring similar methods on iron-rich copper mine waste, led by Prof Southam and including Hamilton and Paterson, was recently published in the Journal of Geochemical Exploration.